Workplace accidents are a significant concern for both employees and employers. According to the International Labour Organization (ILO), over 2.78 million people die annually due to work-related accidents or diseases. Millions more suffer from non-fatal accidents that lead to injuries or long-term health problems. These incidents can result in lost wages, reduced productivity, and increased costs for employers due to medical expenses, legal fees, and compensation claims. However, many of these accidents can be prevented through proper training.
Effective workplace training plays a crucial role in reducing accidents by equipping employees with the knowledge, skills, and awareness necessary to operate safely within their work environment. In this blog, we will explore the connection between proper training and workplace safety, examining various training methods, benefits, and success stories.
# Understanding Workplace Accidents: Causes and Consequences
To appreciate the importance of proper training, it’s essential first to understand the nature and causes of workplace accidents. Accidents in the workplace can occur for various reasons, including:
1. **Lack of Knowledge or Skills**: Employees who are unfamiliar with the proper operation of machinery or equipment are more likely to cause or be involved in accidents.
2. **Inadequate Safety Measures**: When employees are not adequately trained in safety protocols, they may fail to recognize hazards, use protective gear, or follow procedures that could prevent accidents.
3. **Human Error**: Mistakes such as misjudgment, distraction, or fatigue are common causes of accidents and can often be mitigated through comprehensive training that reinforces safe behaviors.
4. **Environmental Factors**: Dangerous working conditions, such as poor lighting, slippery floors, or exposure to hazardous materials, increase the risk of accidents. Employees trained to identify and manage these risks are less likely to be injured.
The consequences of workplace accidents are far-reaching and can include:
– **Injury and Fatality**: Accidents can cause injuries ranging from minor cuts and bruises to life-threatening conditions, permanent disabilities, or fatalities.
– **Productivity Loss**: Injured workers may need time off to recover, which can disrupt operations and decrease productivity.
– **Increased Costs**: Medical expenses, workers’ compensation, and legal fees can burden businesses, particularly smaller companies that may not have the resources to absorb these costs.
– **Reputation Damage**: Repeated accidents can harm a company’s reputation, making it harder to attract new talent and potentially leading to lost business opportunities.
Given these risks, preventing accidents through proper training is essential to maintaining a safe and productive workplace.
# The Role of Proper Training in Reducing Workplace Accidents
Training is the cornerstone of workplace safety. When employees are adequately trained, they become more competent, confident, and aware of potential hazards, significantly reducing the risk of accidents. Here are several ways in which proper training can reduce workplace accidents:
1. **Increased Awareness of Risks and Hazards**
One of the primary purposes of safety training is to raise awareness of workplace hazards. By identifying potential risks, employees can avoid unsafe situations and take proactive measures to mitigate dangers. For example, training might cover topics such as:
– How to identify faulty equipment
– Recognizing hazardous materials and proper handling techniques
– Situational awareness in hazardous environments
Through proper training, employees learn to recognize risks they might have otherwise overlooked, reducing the likelihood of accidents.
2. **Competency in Equipment and Machinery Operation**
Accidents often occur when employees are not fully trained in the operation of machinery or equipment. Whether it’s heavy machinery in construction or sensitive instruments in healthcare, knowing how to use these tools safely is critical. Proper training provides employees with hands-on experience, ensuring they understand how to operate equipment correctly, perform regular maintenance, and respond to malfunctions.
For example, in manufacturing environments, employees may be trained in lockout/tagout (LOTO) procedures, which ensure that machinery is properly shut off and unable to start up again before maintenance or repair work is completed. Such training can prevent serious injuries and fatalities caused by accidental machine start-ups.
3. **Promoting Safe Behavior and Attitudes**
Training not only imparts technical knowledge but also promotes a culture of safety within the workplace. By consistently emphasizing the importance of safety and demonstrating best practices, training helps to reinforce safe behaviors. Employees who are trained regularly are more likely to develop positive attitudes toward safety, encouraging them to follow safety guidelines, wear personal protective equipment (PPE), and avoid shortcuts that could compromise their safety.
Creating this culture of safety fosters collective responsibility, where employees look out for each other and are more willing to report unsafe conditions or behaviors. Over time, this results in fewer accidents and a more positive work environment.
4. **Ensuring Compliance with Regulations and Standards**
Workplace safety is governed by a range of regulations, such as the Occupational Safety and Health Administration (OSHA) standards in the United States, or similar bodies worldwide. These regulations require employers to ensure that employees are trained to understand and comply with safety standards relevant to their industry.
Failure to comply with safety regulations can result in hefty fines and legal penalties, as well as an increased risk of accidents. Proper training ensures that employees are well-versed in regulatory requirements and industry standards, thereby reducing the risk of non-compliance and the associated dangers.
5. **Developing Emergency Response Skills**
No matter how careful an organization is, accidents can still happen. This is why it’s essential for employees to be trained in emergency response procedures. Whether it’s knowing how to evacuate during a fire, providing first aid to an injured colleague, or containing a chemical spill, emergency preparedness can significantly reduce the severity of accidents.
Proper training equips employees with the skills to respond quickly and effectively in an emergency, potentially saving lives and preventing further damage or injury. Regular drills and refresher courses help to keep these skills sharp and ensure that employees are prepared to act when needed.
6. **Reducing Human Error**
While human error is often unavoidable, proper training can significantly reduce the frequency and impact of mistakes. Training helps employees develop better judgment, improves decision-making skills, and reinforces the importance of focus and attention to detail.
For instance, fatigue management training can help employees recognize when they are too tired to work safely, encouraging them to take breaks or avoid high-risk tasks until they are alert again. Similarly, mindfulness training can help employees stay present and focused, reducing the likelihood of distraction-related accidents.
# Effective Training Methods for Workplace Safety
Not all training is created equal, and the effectiveness of a training program depends on its design and delivery. Here are some proven methods for enhancing workplace safety through training:
1. **On-the-Job Training**
On-the-job training allows employees to learn in real-world conditions under the guidance of experienced colleagues or supervisors. This method is particularly effective for jobs that require hands-on skills, such as operating machinery, handling hazardous materials, or working in construction. By practicing tasks in a controlled environment, employees gain the experience they need to perform safely on the job.
2. **Classroom-Based Training**
Classroom-based training provides a structured environment for employees to learn about safety protocols, regulations, and best practices. This method is useful for imparting theoretical knowledge, such as safety regulations, emergency procedures, or the principles of ergonomics. Classroom sessions can include lectures, videos, group discussions, and role-playing exercises to engage learners and reinforce key concepts.
3. **Online Training**
Online training, also known as e-learning, is a flexible and cost-effective way to deliver safety training to employees. This method is particularly useful for companies with dispersed workforces, as employees can complete training modules at their own pace from any location. Online training can cover a wide range of topics, from basic safety principles to more specialized areas such as cybersecurity or chemical safety.
4. **Simulations and Virtual Reality (VR)**
Simulation-based training uses realistic scenarios to help employees practice their skills in a safe and controlled environment. This method is particularly useful for high-risk jobs, such as firefighting, aviation, or surgery, where mistakes in real-life settings can have catastrophic consequences. Virtual reality (VR) takes simulations a step further by immersing employees in a 3D environment, allowing them to interact with simulated hazards and practice responses in real time.
5. **Refresher Training and Drills**
Safety training should not be a one-time event. Regular refresher courses and drills help employees retain their knowledge and keep their skills sharp. Drills are especially important for emergency preparedness, as they allow employees to practice their response to various scenarios, such as fires, chemical spills, or workplace violence.
# Success Stories: How Training Reduces Accidents
Numerous organizations across various industries have demonstrated the effectiveness of proper training in reducing workplace accidents. Here are a few success stories:
– **Caterpillar Inc.**: This multinational manufacturing company is known for its comprehensive safety training programs. Caterpillar has implemented a “Zero-Injury Safety Program” that focuses on leadership commitment, employee engagement, and continuous training. As a result, the company has seen a significant reduction in workplace injuries and accidents over the years.
– **BP**: Following a major safety incident, BP invested heavily in safety training and culture change. The company implemented a rigorous safety management system and provided employees with extensive training in hazard recognition, emergency response, and safe work practices. These efforts have contributed to a marked improvement in safety performance, particularly in its offshore operations.
– **Tesla**: Tesla’s Gigafactories are known for their high-tech manufacturing processes, but the company also places a strong emphasis on safety training. Tesla has implemented a robust safety training program that includes regular safety briefings, on-the-job training, and incident drills. As a result, the company has been able to maintain a lower-than-industry-average injury rate.
Conclusion: Investing in Safety Training Pays Off
Proper training is not just a legal obligation for employers; it is a moral responsibility and a smart business investment. By equipping employees with the knowledge, skills, and awareness necessary to operate safely, organizations can significantly reduce the risk of accidents, improve productivity,
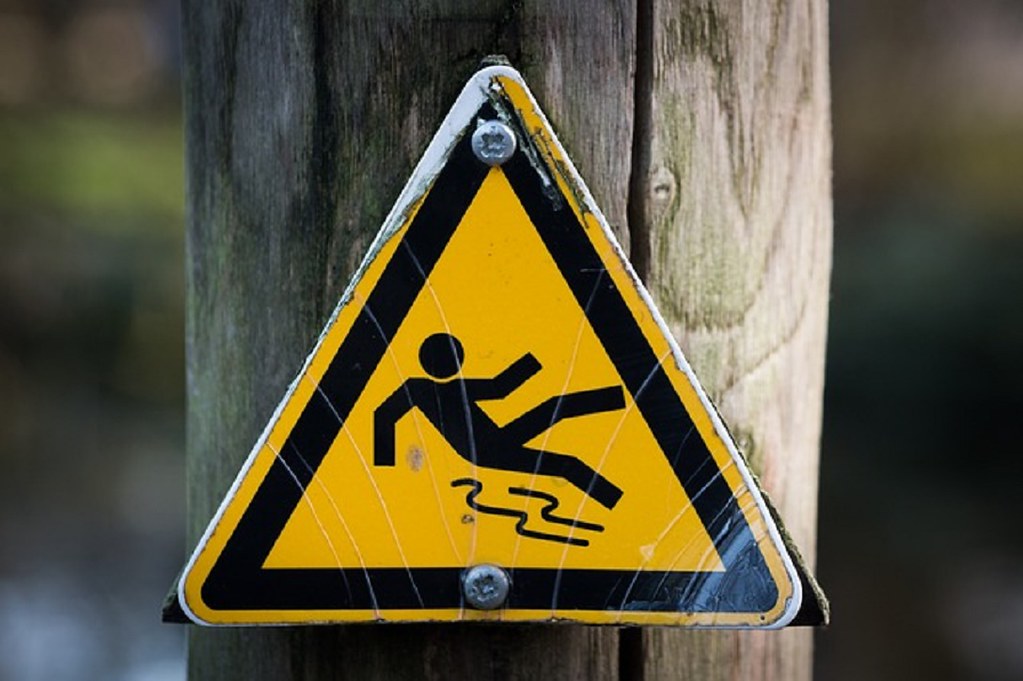