In today’s competitive business landscape, product quality has become a critical differentiator for companies across industries. While factors such as technology, process optimization, and quality control measures play significant roles in enhancing product quality, one often overlooked aspect is the importance of employee training. This blog post explores the crucial role that training plays in improving product quality and how organizations can leverage it to gain a competitive edge.
Understanding the Link Between Training and Product Quality
At its core, product quality is a reflection of the skills, knowledge, and dedication of the workforce involved in its creation. From design and development to manufacturing and quality control, every stage of the product lifecycle is influenced by the competencies of the employees involved. This is where training becomes a pivotal factor in driving quality improvements.
Training serves multiple purposes in the context of product quality:
1. Skill Enhancement: It equips employees with the necessary skills to perform their jobs more effectively and efficiently.
2. Knowledge Transfer: It ensures that best practices, industry standards, and company-specific processes are communicated and understood across the organization.
3. Error Reduction: Proper training helps minimize human errors that can lead to quality issues.
4. Continuous Improvement: It fosters a culture of learning and improvement, encouraging employees to seek out ways to enhance product quality.
5. Adaptability: Training helps employees stay current with evolving technologies, market demands, and quality standards.
Key Areas Where Training Impacts Product Quality
1. Technical Skills Development
One of the most direct ways training influences product quality is through the development of technical skills. This is particularly crucial in industries where product complexity is high, such as manufacturing, technology, and healthcare. Technical training programs can cover a wide range of topics, including:
– Operating machinery and equipment
– Understanding and implementing quality control processes
– Utilizing software and digital tools effectively
– Applying industry-specific techniques and methodologies
By enhancing these technical skills, organizations can significantly reduce defects, improve precision, and increase overall product reliability.
2. Quality Management Systems and Standards
Training plays a vital role in implementing and maintaining quality management systems (QMS) such as ISO 9001, Six Sigma, or Total Quality Management (TQM). These systems provide frameworks for ensuring consistent product quality, but their effectiveness relies heavily on employee understanding and adherence.
Training programs focused on quality management should cover:
– Principles and practices of the chosen QMS
– Role-specific responsibilities within the quality framework
– Documentation and reporting procedures
– Continuous improvement methodologies
When employees are well-versed in these areas, they can more effectively contribute to maintaining high quality standards throughout the production process.
3. Soft Skills and Communication
While technical skills are crucial, soft skills also play a significant role in product quality. Effective communication, teamwork, problem-solving, and critical thinking are all essential for maintaining high quality standards. Training programs that address these soft skills can lead to:
– Improved collaboration between departments, resulting in better-aligned processes
– Enhanced problem-solving capabilities, allowing for quicker identification and resolution of quality issues
– More effective communication of quality requirements and feedback throughout the organization
4. Safety and Compliance
In many industries, product quality is closely tied to safety and regulatory compliance. Training in these areas ensures that employees understand and follow safety protocols and regulatory requirements, which directly impacts product quality and consumer safety.
Key aspects of safety and compliance training include:
– Industry-specific regulations and standards
– Proper handling of materials and equipment
– Documentation and traceability requirements
– Risk assessment and mitigation strategies
By prioritizing safety and compliance training, organizations not only improve product quality but also mitigate risks associated with non-compliance and potential safety hazards.
5. Customer Focus and Market Awareness
Understanding customer needs and market trends is crucial for delivering high-quality products that meet or exceed expectations. Training programs that focus on customer-centricity and market awareness can significantly impact product quality by:
– Aligning product features with customer preferences
– Anticipating and addressing potential quality issues before they reach the customer
– Fostering a culture of customer satisfaction throughout the organization
This type of training helps employees understand the “why” behind quality standards and encourages them to take ownership of product quality.
Implementing Effective Training Programs for Quality Improvement
To maximize the impact of training on product quality, organizations should consider the following strategies:
1. Needs Assessment and Tailored Training
Before implementing any training program, it’s essential to conduct a thorough needs assessment. This involves:
– Identifying skill gaps within the organization
– Analysing quality data to pinpoint areas for improvement
– Gathering feedback from employees and managers
Based on this assessment, organizations can develop tailored training programs that address specific quality-related challenges and skill deficiencies.
2. Blended Learning Approaches
Effective training programs often utilize a mix of learning methodologies to cater to different learning styles and maximize knowledge retention. A blended learning approach might include:
– Classroom-based instruction for theoretical concepts
– Hands-on practical sessions for skill development
– E-learning modules for self-paced learning
– Virtual reality simulations for complex or high-risk scenarios
This multi-faceted approach ensures that employees receive comprehensive training that translates effectively to their day-to-day responsibilities.
3. Continuous Learning and Refresher Courses
Quality improvement is an ongoing process, and training should reflect this. Implementing a continuous learning culture through regular refresher courses and updates helps:
– Reinforce key quality concepts and best practices
– Keep employees informed about changes in industry standards or company processes
– Provide opportunities for skill refinement and advancement
4. Measuring Training Effectiveness
To ensure that training programs are genuinely impacting product quality, it’s crucial to establish metrics for measuring their effectiveness. Some key performance indicators (KPIs) to consider include:
– Reduction in defect rates or quality issues
– Improvement in customer satisfaction scores
– Increased productivity or efficiency in quality-related processes
– Employee feedback and self-assessment of skill improvement
Regularly reviewing these metrics allows organizations to refine their training programs and focus resources on the most impactful areas.
5. Leadership Involvement and Support
The success of any training initiative largely depends on the support and involvement of leadership. When leaders actively participate in and advocate for quality-related training, it sends a strong message about the organization’s commitment to product excellence. This involvement can take various forms:
– Executive sponsorship of training programs
– Leadership participation in select training sessions
– Regular communication about the importance of quality and ongoing learning
Overcoming Challenges in Training for Quality Improvement
While the benefits of training for quality improvement are clear, organizations often face challenges in implementing effective programs. Some common obstacles include:
1. Resource Constraints
Quality-focused training can be resource-intensive, requiring investments in time, money, and personnel. Organizations may struggle to allocate sufficient resources, especially when facing budget constraints or production pressures.
Solution: Prioritize training initiatives based on their potential impact on quality and ROI. Consider leveraging internal experts for knowledge sharing and exploring cost-effective e-learning solutions.
2. Resistance to Change
Employees may resist new training initiatives, especially if they feel it disrupts their established routines or if they don’t see the immediate benefits.
Solution: Communicate the importance and benefits of training clearly. Involve employees in the training design process and provide incentives for participation and application of new skills.
3. Measuring Long-term Impact
While short-term improvements may be evident, it can be challenging to attribute long-term quality enhancements directly to training initiatives.
Solution: Establish a robust system for tracking quality metrics over time. Conduct regular assessments to correlate training efforts with quality improvements and adjust programs accordingly.
4. Keeping Training Content Relevant and Up-to-date
In rapidly evolving industries, training content can quickly become outdated, reducing its effectiveness in improving product quality.
Solution: Establish a regular review process for training materials. Collaborate with industry experts and leverage feedback from employees to ensure content remains relevant and aligned with current best practices.
The Future of Training in Quality Improvement
As technology continues to advance and market demands evolve, the role of training in quality improvement is likely to become even more critical. Some emerging trends to watch include:
1. AI and Machine Learning in Training
Artificial Intelligence and Machine Learning technologies are beginning to play a significant role in personalizing training experiences and predicting skill gaps before they impact product quality.
2. Virtual and Augmented Reality
These technologies offer immersive training experiences that can simulate complex quality control scenarios without the risks associated with on-the-job learning.
3. Microlearning and Just-in-Time Training
Bite-sized learning modules delivered at the point of need are becoming increasingly popular, allowing employees to access relevant training exactly when they need it.
4. Cross-functional and Supply Chain Training
As product ecosystems become more complex, training programs that address quality across entire value chains and encourage cross-functional collaboration are likely to gain prominence.
Conclusion
The role of training in improving product quality cannot be overstated. By investing in comprehensive, well-designed training programs, organizations can enhance technical skills, foster a culture of quality, and drive continuous improvement. As markets become increasingly competitive and consumer expectations continue to rise, those companies that prioritize training as a key component of their quality strategy will be best positioned to succeed.
Effective training not only improves immediate product quality but also builds a foundation for long-term success. It empowers employees to take ownership of quality, fosters innovation, and creates a workforce capable of adapting to future challenges. In essence, training is not just about teaching skills; it’s about cultivating a mindset where quality is everyone’s responsibility.
As we look to the future, the organizations that recognize training as a strategic investment rather than a mere operational requirement will be the ones that consistently deliver high-quality products, earn customer loyalty, and maintain a competitive edge in their industries.
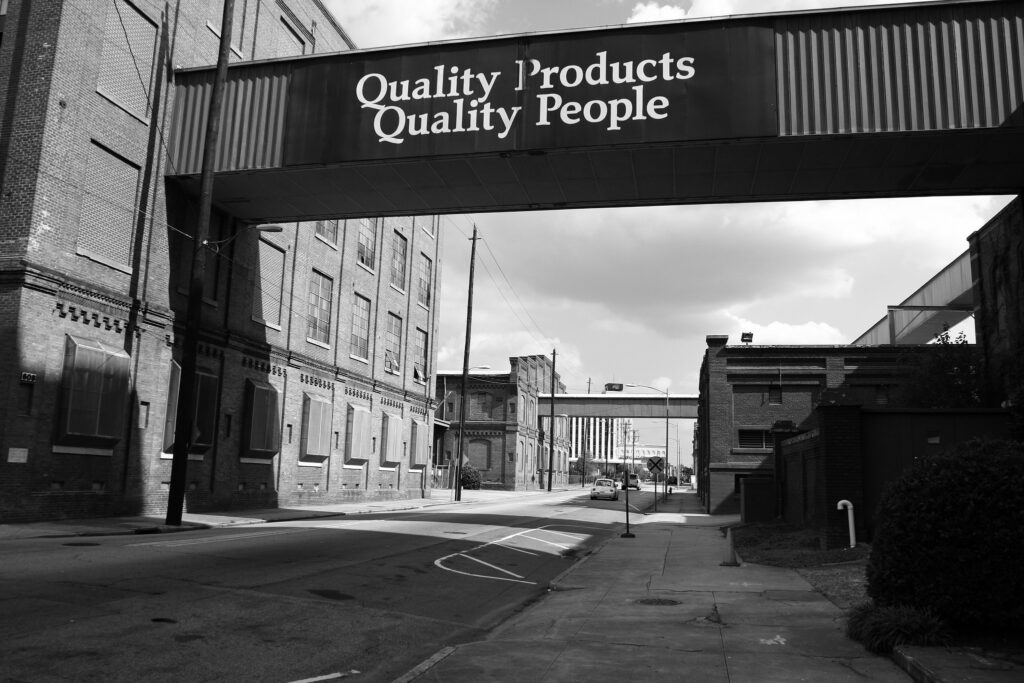